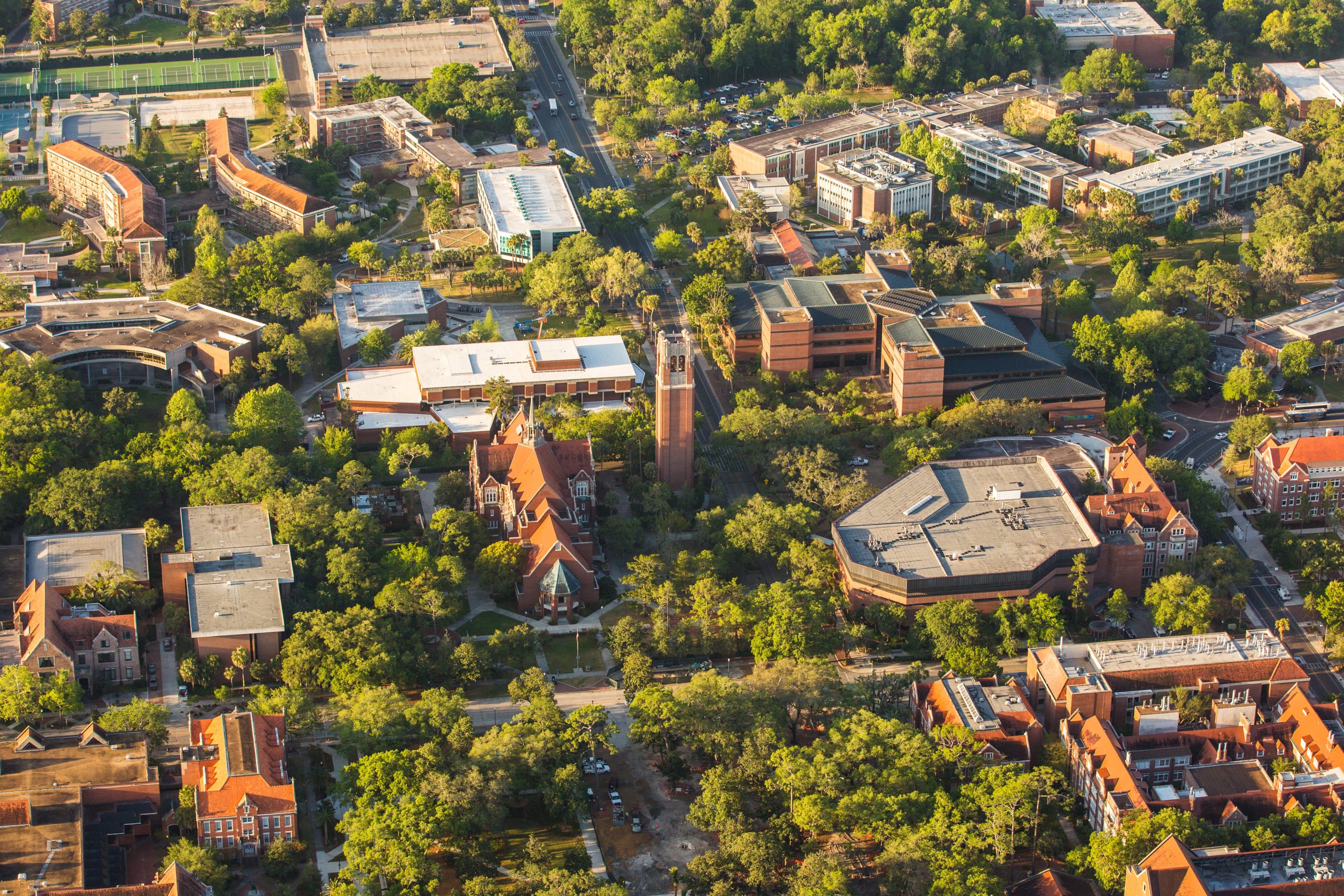
Fall Protection Policy
OBJECTIVE
To protect employees by reducing the risk of injury or fatality from falls from height or on the same level.
POLICY
All employees, students, volunteers and contractors working under direct UF supervision shall comply with all elements of the UF Fall Protection Program.
AUTHORITY
By authority delegated from the University President, the Vice-President for Business Affairs is responsible for the safety of all University facilities. Under this authority, policies are developed to provide a safe teaching, research, service, housing and recreational environment.
RESPONSIBILITIES
- a person who is capable of identifying existing and predictable hazards in the surroundings or identifying working conditions which are hazardous or dangerous to employees and
- who has authorization to take prompt corrective measures to eliminate them.
Employees are responsible for wearing the appropriate fall protection equipment when directed and for following the procedure specified in this policy. Employees are responsible for the proper care, use and inspection of their assigned fall protection equipment. Employees are expected to report any unsafe conditions to a supervisor.
PROCEDURES
Supervisors or other designated staff must conduct regular inspections to identify slip, trip and fall hazards and to ensure walking and working surfaces are maintained in a safe condition.
All areas of a workplace and walking and working surfaces must be kept clean, orderly, dry and in sanitary condition.
All work performed from elevated surfaces including roofs, building ledges, mobile lifts, scaffolding and other work platforms shall be in accordance with this policy and with the following Fall Protection Program
FALL PROTECTION PROGRAM
An employee must be protected from falling when working on a surface that has an unprotected side or edge which is 6 feet or more above an adjacent lower level or when working from aerial lifts or other elevated work platforms and lifts.
In each of these cases, the fall hazards must be evaluated to determine the preferable method to protect the employee. When considering what type of fall protection to use, the following hierarchy of remedies, in order of preference, should be considered:
- Elimination of the fall hazard by bringing the work down to safe ground level
- Use of passive fall protection systems such as guard rails
- Fall restraint which prevents a person from reaching a fall hazard
- Fall arrest which utilizes equipment to stop a fall after it occurs
- Administrative controls which use work practices or procedures to signal or warn a worker to avoid approaching a fall hazard.
The competent person must train employees in the following areas:
- fall hazards in the work area
- correct procedures for erecting, maintaining, disassembling and inspecting the fall protection systems used
- selection, proper use and care of equipment comprising a personal fall arrest system
- role of employees in fall protection plans
- what rescue procedures to follow in case of a fall
- overview of the OSHA fall protection standards
A training record shall be maintained for each employee. The record will contain the name of the employee trained, date of training and the signature of the person who conducted the training. Retraining shall be required every two years and if there is a change in the fall protection system being used or if an employee’s actions demonstrate that the employee has not retained the understanding or skills important to fall protection.
Guardrails are needed at the edge of work areas 6 feet or more in height to protect employees from falling. This includes the edge of excavations greater than six feet in depth. Guardrail systems need to meet the following criteria:
- Toprail is 42 inches, +/- 3 inches above the walking/working level
- Midrail is located midway between the top rail and the walking/working level
- It is important to remember that the working level is that level where the work is being done. Someone working on a stepladder next to an edge may raise his/her working surface well above the walking surface.
- Both top and midrails should be constructed of materials at least one-quarter inch in thickness or diameter. If wire rope is used for toprails, it needs to be flagged with a high-visibility material at least every 6 feet and can have no more than 3” of deflection
- The toprail needs to withstand a force of 200 pounds when applied in any downward or outward direction.
- The midrail needs to withstand a force of 150 pounds applied in any downward or outward direction
- Toeboards are required for all guardrails on elevated walking or working platforms where employees working below are exposed to falling objects. Toeboards must be four inches in height and must be securely fastened.
- The system should be smooth to prevent punctures, lacerations or snagging of clothing
- The ends of the top rail shouldn’t overhang the terminal posts, except when such overhang does not present a projection hazard
- When a hoisting area is needed, a chain, gate or removable guardrail section must be placed across the access opening when hoisting operations are not taking place.
Skylights constructed at least 42 inches above the roof deck with sides capable of supporting 200 pounds do not require additional protection.
There are three main components to the personal fall arrest system. This includes the personal protective equipment the employee wears, the connecting devices and the anchorage point. Prior to tying off to perform the work a means of rescue in the event of a fall must be immediately available. All personal fall arrest system components must meet the requirements of the ANSI Z359 Standards. The system needs to meet the following criteria for each component:
- Full body harnesses are required. The use of body belts is prohibited.
- The attachment point of the body harness is the center D-ring on the back.
- Employees must always tie off at or above the D ring of the harness except when using lanyards 3 feet or less in length.
- Harnesses or lanyards that have been subjected to an impact load shall be destroyed.
- Load testing shall not be performed on fall protection equipment.
- Only locking snaphooks may be used.
- Horizontal lifelines will be designed by a qualified person and installed in accordance with the design requirements.
- Lanyards and vertical lifelines need a minimum breaking strength of 5,000 pounds.
- The length of a single lanyard shall not exceed six feet.
- The use of steel lanyards is prohibited.
- Lanyards may not be clipped back to itself (e.g. around an anchor point) unless specifically designed to do so.
- If vertical lifelines are used, each employee will be attached to a separate lifeline.
- Lifelines need to be protected against being cut or abraded
- Structure must be sound and capable of withstanding a 5000 lb. static load.
- Structure/anchor must be easily accessible to avoid fall hazards during hook up.
- Direct tying off around sharp edged structures can reduce breaking strength by 70% therefore; chafing pads or abrasion resistant straps must be used around sharp edged structures to prevent cutting action against safety lanyards or lifelines.
- Structures used as anchor points must be at the worker’s shoulder level or higher to limit free fall to 6 feet or less and prevent contact with any lower level (except when using a self-retracting lifeline or 3 foot lanyard).
- Choose structures for anchor points that will prevent swing fall hazards. Potentially dangerous “pendulum” like swing falls can result when a worker moves horizontally away from a fixed anchor point and falls. The arc of the swing produces as much energy as a vertical free fall and the hazard of swinging into an obstruction becomes a major factor. Raising the height of the anchor point can reduce the angle of the arc and the force of the swing. Horizontal lifelines can help maintain the attachment point overhead and limit the fall vertically. A qualified person must design a horizontal lifeline.
- Environmental factors and dissimilarity of materials can degrade exposed anchors.
- Compatibility of permanent anchors with employee’s fall arrest equipment.
- Inclusion of permanent anchors into a Preventive Maintenance Program with scheduled annual re-certification.
- Visibly label permanent anchors.
- Roof anchors must be immediately removed from service and re-certified if subjected to fall arrest forces.
- Reusable temporary roof anchors must be installed and used following the manufacturer’s installation guidelines.
- Roof anchors must be compatible with employee’s fall arrest equipment.
- Roof anchors must be removed from service at the completion of the job and inspected prior to reuse following the manufacturer’s inspection guidelines.
- Roof anchors must be immediately removed from service and disposed of if subjected to fall arrest forces.
- If a fall occurs, the employee should not be able to free fall more than 6 feet nor contact a lower level.
- To ensure this, add the height of the worker, the lanyard length and an elongation length of 5.5 feet. Using this formula, a six-foot worker would require a tie-off point at least 15.5 feet above the next lower level.
- A personal fall arrest system that was subjected to an impact needs to be removed from service immediately.
- Personal fall arrest systems need to be inspected prior to each use and damaged or deteriorated components removed from service.
- Personal fall arrest systems should not be attached to guardrails or hoists.
Body harnesses must be worn with a shock-absorbing lanyard (preferably not to exceed 3 feet in length) and must be worn when working from an elevated work platform (exception: scissor lifts and telescoping lifts that can move only vertically do not require the use of a harness and lanyard as long as the work platform is protected by a guardrail system). The point of attachment must be the anchor point installed by the equipment manufacturer. Personnel cannot attach lanyards to adjacent poles, structures or equipment while they are working from the aerial lift.
Personnel cannot move an aerial lift while the boom is in an elevated working position and the operator is inside of the lift platform.
A note specific to work performed 15 feet or more from a roof edge:
No fall protection is required when the work is infrequent and temporary. As a matter of policy, employees are prohibited from going within 15 feet of a roof edge without the use of fall protection.
Infrequent and temporary refer to work that is performed only occasionally and for a brief or short time. Annual equipment maintenance and HVAC filter changes are covered by this definition.
Appendix A – Personal Fall Arrest System Inspection
Harness Inspection
- Snaps: Inspect closely for hook and eye distortions, cracks, corrosion, or pitted surfaces. The keeper (latch) should seat into the nose without binding and should not be distorted or obstructed. The keeper spring should exert sufficient force to firmly close the keeper. Keeper locks must prevent the keeper from opening when the keeper closes.
- Thimbles: The thimble must be firmly seated in the eye of the splice, and splice should have no loose or cut strands. The edges of the thimble must be free of sharp edges, distortion, or cracks.
- The lanyard housing must be inspected to ensure that casing bolts are tight and that there are no loose fasteners, missing parts, cracks or excessive wear or corrosion.
- Webbing must be inspected for cuts, nicks or tears as well as for any broken fibers, stitching or fraying.
- Steel lanyards should be inspected for cuts, fraying, broken wires and overall deterioration and excessive wear.
- Fittings are to be inspected for wear or cracks and obvious damage.
- Follow manufacturer’s recommendations for additional inspection tasks and for any requirements that the unit be sent in to the manufacturer for periodic inspection.